EQUIPMENT
Installation and welding work is carried out with modern equipment and welding technologies, which ensures the stability and reliability of the construction work. "NEFTGAZMONTAJ" LLC owns the most advanced equipment for automatic welding of non-stop joints in inert gas environment (Argon-CO2) CRC-EVANS Automatic Welding. Equipped with a machine for machining the edges of PFM, internal centralizer with built-in automatic welding heads for making the root pass from the inside, 8 external automatic welding two-arc heads P600 (latest version) with two burners for filling and facing layers of the seam.
There is an integrated team for welding non-rotating pipes joints, lashes on the track by means of the STT + M300C method. Integrated team for assembling, bounding of line valve stations and welding of overlaps, transitions through artificial and natural obstacles, rotation angles, receiving and launching stations, etc. by the STT + Innershield method.
For production of bent pipes, a mobile pipe bending machine PB 3848 is used for cold bending of pipes with applied insulation.
CRC – Evans Complex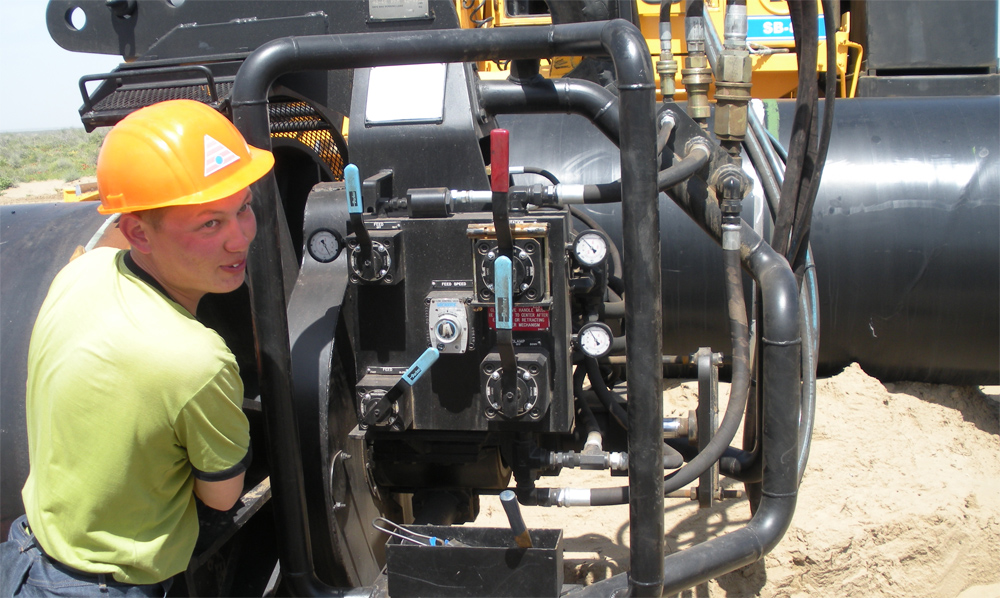
The newest high-tech welding complex CRC-Evans automatic welding from CRC company for automatic welding of non-stop joints in inert gases (Argon-CO2). This complex is the first in the Republic of Uzbekistan and the only one in Central Asia. The automatic welding complex is equipped with machines for mechanical edge processing (PFM), a self-propelled internal centralizer - a welding station with built-in automatic welding heads for making the root layer from inside the pipe, 8 external automatic welding heads P-600 (representative of a new generation of external welding heads with two independent Burners) for filling and covering layers of the seam. The heads of the P-600 provide higher deposition in one pass and significantly increase the welding speed due to the use of two independent burners. A computerized welding system with two burners allows the self-control of welding quality by continuously recording the parameters of the welding process. The use of this complex allowed to provide high quality of welding from the joint to the joint, to achieve qualitative and stable parameters of the mechanical properties of the welded joint, the stability of the welding quality with minor errors of the operator-welder and increase in productivity from 40 to 100 joints per shift. The above-mentioned "NEFTGAZMONTAJ" welding complex on the construction of the international gas pipeline "Uzbekistan-China" first welded 210 km in the shortest time and with high quality welding. The average productivity per shift was 50 joints.
For successful operation of the automatic welding complex CRC-Evans, "NEFTGAZMONTAJ" LLC has sent its welding operators in two groups (1st group - 19 people, 2nd group - 20 people) and welders of mechanized welding Innershield (group of 12 people) for training in the specialized training center of the city Gagarin of the Smolensk region. Welding operators, consisting of 16 people, aimed to work for a semi-automatic welding complex STT + M300 completed training and internship by highly qualified specialists with a wide experience, directly at the construction site (track). All operators are welders who received the training certificates were evaluated and attested by independent inspectors of "MOODY International" in accordance with the rules of attestation of welders for the international project of construction of the gas pipeline "Uzbekistan China".
The electric welders of manual arc welding, have been certified to a group of pipe diameters. They can make all-position welding by electrodes with the main type of coating and method of lifting. In addition, in Amirabad industrial base, there are qualification upgrading courses organized for electric welders.
STT + M 300 Complex
The two newest and modern semi-automatic welding complexes, first introduced by our company on the territory of the Republic of Uzbekistan are: STT + M300C jointly developed by Lincolnelectric and CRC-Evans for the welding of nonrotative pipe joints and lashings on the track. Semiautomatic welding systems are equipped with mechanized feeding devices for welding wire LF-37 and welding current sources Invertec STT II for welding of the root pass in CO2 and 10 by external automatic torches M300C for filling and facing layers in an atmosphere of shielding gas (argon-CO2). These semi-automatic welding systems allow the use of standard factory cutting with a bevel angle of 30 degrees and standard dulling. Welding technology STT ensures the production of high-quality root pass of the seam. Computerized welding heads M300C are portable, almost universal and easy to operate. These complexes were used in the welding of gas pipelines: "CAC-2"; CAC-4 "; "Ahangaran-Pungan through the Kamchik Pass"; "Uzbekistan-China".
Innershield complex
Mechanized welding by Innershield FCAW wire. The advantage of FCAW wire is that it has a high build-up ratio and does not require the use of protective gas. The Innershield mechanized welding kit includes a mobile wire-drive unit LN-23P complete with a K-350 adapter and a welding blowpipe assembled with a cable (K345-10 kit with a dual-mode switch).
Pipe welding stations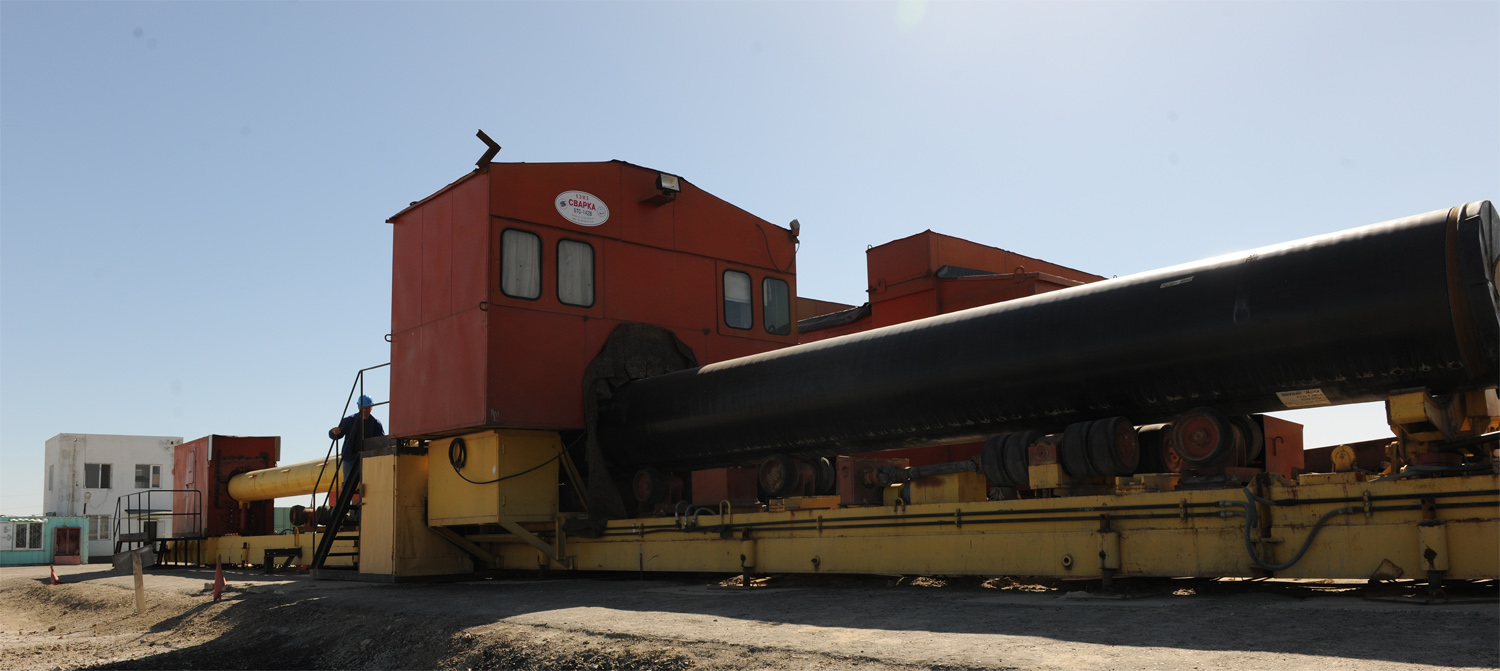
Automatic installation of "BTS-142V" equipped with automatic welding heads A2, A6 for welding under a flux layer and rectifiers "LAF 1000", "LAF 1250" manufactured by ESAB company and adapted for work with welding materials made in CIS countries, as well as for non-CIS states. The advantages of the "BTS 142B" are:
- Low defects rate (due to lack of manual welding, stability of welding quality with minor errors of the operator - welder);
- the entire welding process takes place without section shift;
- minimum number of staff
Semiautomatic apparatus "BTS-142V" is specialized for two-sided automatic welding under the flux layer of two and three pipe sections with preliminary preparation of the pipe edges in the field conditions on the pipe welding base during the construction of pipelines. The productivity of the pipe-welding base is up to 25 joints per shift.
Semiautomatic apparatus "PAU-1001V" with the assembly stand "SST-141" completed with welding equipment ESAB (welding heads A6 and rectifiers LAF 1250) with adaptation of the use of welding materials both imported and CIS countries. Assembly and manual arc welding of the root layer of the seam is performed on the assembly stand "SST 141". Then, on special slides, it is fed to the intermediate rack for manual arc welding of the infusion layer. Then, also on special slides, the sections are transferred to the field automatic welding machine "PAU-1001B" for automatic welding under the flux layer with welding head A6 from ESAB filling and facing seam layers. The productivity of the pipe-welding base is up to 15 joints per shift.
Pipe bending machine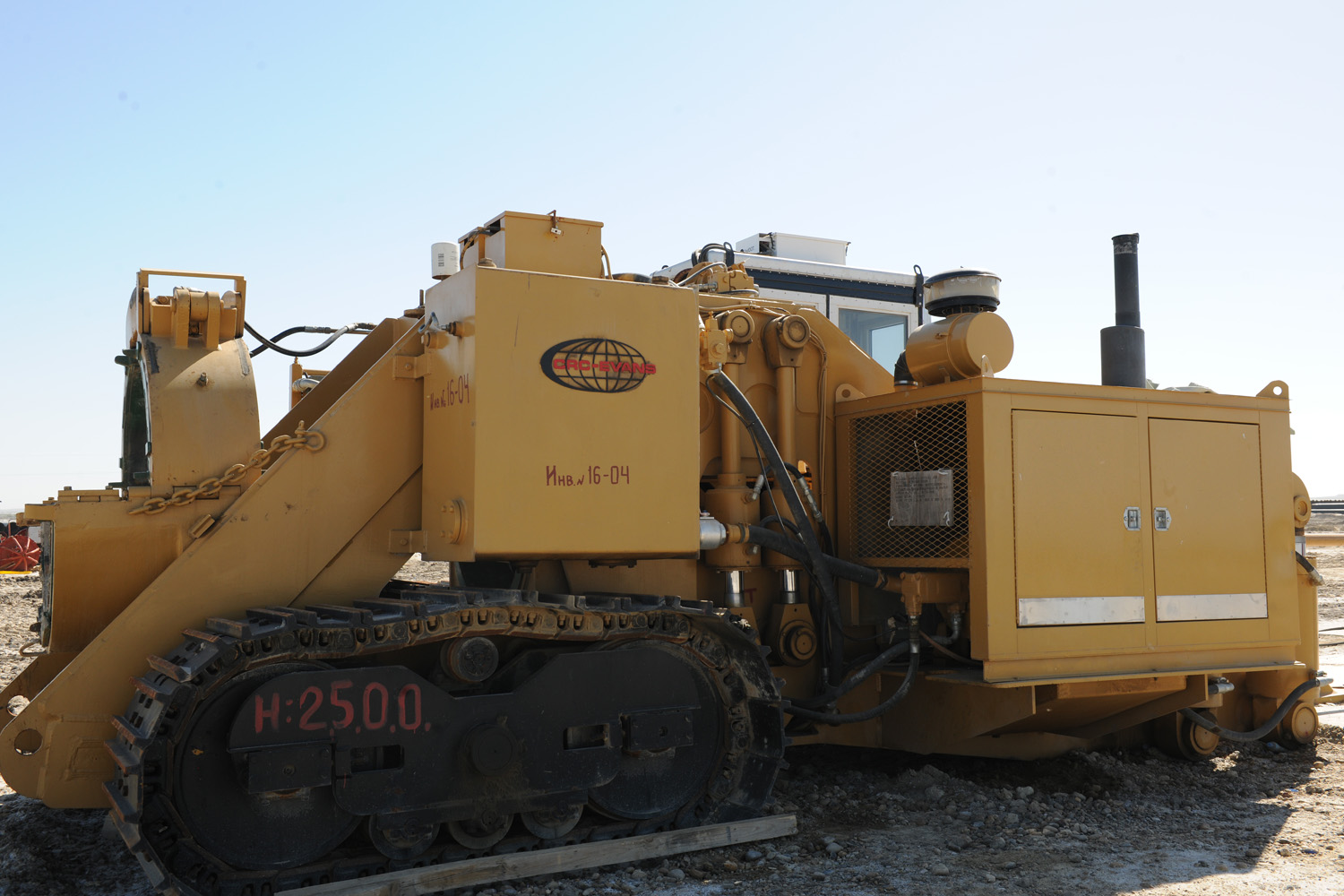
Vertical hydraulic pipe bending machine "PB3848" for cold bending pipes with a factory anti-corrosion coating and diameter of 864 - 1220 mm, driven by a diesel engine. The machine is equipped with a power take-off system for power supply of hydraulic mandrel. It is mounted on steel tracks and is designed for operation in temperature conditions up to -20 ° C. The pipe bending machine is specialized for manufacturing curves up to 5 ° directly at the site of construction and assembly operations on the track.
Horizontal drilling
Installation of horizontal drilling machine "PD 250/90 RP"
Installation of horizontal drilling machine "PD 250/90 RP" produced by PRIMEDRILLING Company. This facility is the first in the Republic of Uzbekistan and the unique one in Central Asia. This installation allows the construction of pipeline crossings through water, natural and artificial obstacles by a progressive horizontal directional drilling method (HDD).
Works completed on HDD:
1. This machine was used to complete the construction of double pipeline crossings through the Amu Darya, near Khodjeyli settlement, on "Gazli-Nukus" gas pipeline Ø 1020mm, each 814 meters long. The works on wells drilling and sweeping-up, as well as drawing of pipeline siphons into prepared wells were successfully completed. Borehole wall lining is carried out by using the ecologically friendly polymeric clay mortar - bentonite. The actual profile of the drilled wells practically duplicated the designed ones, the accuracy of reaching the spot was very high. The depth of the wells was 17 m beneath the surface of the river bottom and 21 m from the entry point.
2. The construction of the gas pipeline transition piece Ø325mm of the medium pressure in a case Ø530mm through 13 railway tracks along the M. Torobiy and T. Avezova streets, in Cagan, city Bukhara region, with the extent of 200 m by HDD method.
Construction period: August - September 2010.
Project owner: "Uztransgazinzhinering" Stock Company.
The work was carried out by horizontal directional drilling method and by PD250/90RP HDD machine. It was conducted in tight urban conditions, with a dense network of complex underground communications, as well as without interruption of railway traffic. This kind of work with the use of advanced technologies was conducted in Uzbekistan for the first time. The work was completed qualitatively and on time. It should be noted that all stages of complex work for the first time were carried out independently by the specialists of "Neftgazmontazh" LLC without the intervention of foreign specialists.
3. Construction by the HDD method of the crossover of the gas reservoir Ø 406mm and fuel gas Ø 57mm under the strait of Lake Dengizkul with the length of 600m each, according to the project "Construction of the Shoda Dengizkul field".
Project owner: JV LLC "Lukoil Uzbekistan"
General constructor: JV LLC "ERIELLCorporation SRO"
Construction period: July - October 2011.
The work was carried out in difficult geological conditions of the region: sands, barkhans, impassability, sandy rocks all this complicated the process of horizontally directed drilling. Compared with other methods of laying gas pipelines through water barriers, over long distances, the HDD method is the most progressive and economical solution. Our works were well appreciated by the specialists of LUKOIL and ERIELL. The implementation of such types of work using horizontal directional drilling equipment, with a pulling capacity of 250 tons, has no analogues in our region
Groove preparation
The machines for groove preparation of pipes "SPK 124" in the amount of 2 pcs. are used in "NEFTGAZMONTAJ" to restore the factory edge of pipes with a diameter of 1020 -1220 mm after gas cutting in the field directly at the pipeline construction site.
Welding machines:
" ХТЗ АС 42А" - 22 units, "LIEBHERR SR 712 B" - 8 units, "AST-4A" (based on the crawler track TT-4M) - 6 units, "АС-81А (К-701)" - 2 pieces.
Total amount - 66 units.